Hidden Structural Defects: What Do Building and Structural Surveys Uncover?
A technical survey of buildings and structures is a vital process for determining their structural integrity and identifying potential safety risks. It's particularly crucial when a property is being considered for renovation, major alteration, or purchase. Often, defects aren't immediately obvious – they're 'hidden', and their impact on load-bearing elements or the building's longevity can be considerable. In this article, we'll delve into the technical survey methods employed and the most common faults found in various types of buildings across Latvia.
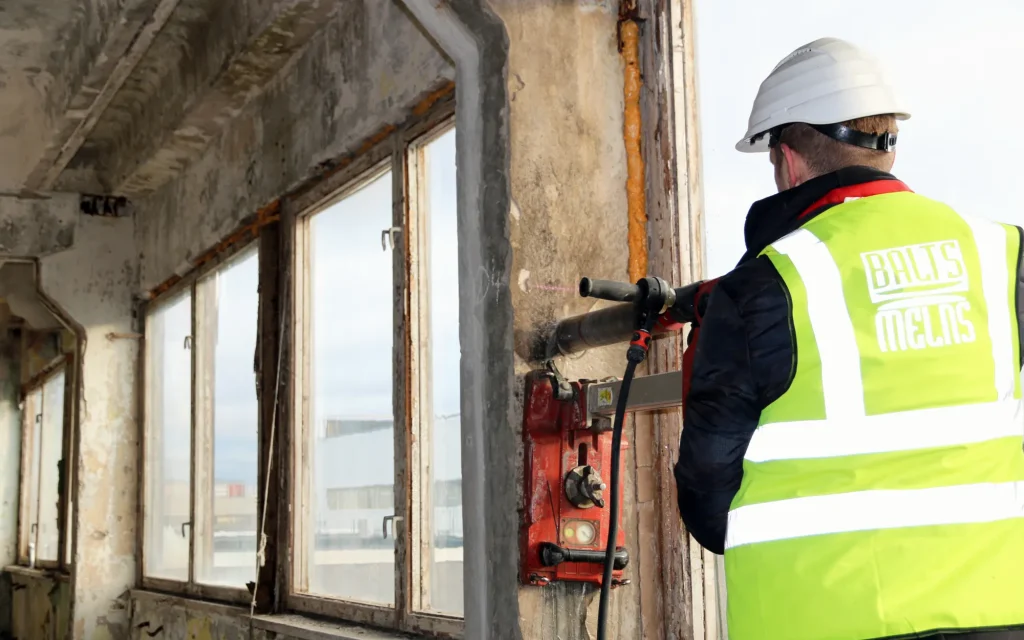
Building Technical Survey Methods
A technical survey of buildings and structures involves an in-depth assessment of the condition of a building's load-bearing and enclosing structures, building services, and other essential elements. This is carried out by a certified building professional. The aim of such a survey is to objectively determine the building's technical condition, identify existing or potential defects, and assess their impact on the building's safety, structural integrity, and serviceability. It also provides recommendations for necessary remedial works or strengthening. To gain a comprehensive understanding of a building's condition, experts employ various methods.
Lai iegūtu pilnvērtīgu ainu par ēkas stāvokli, eksperti izmanto dažādas metodes.
Visual Inspection
This remains the primary method, but an expert's eye spots what a layperson might miss – subtle deformations, the specific nature of cracks that can indicate a particular problem (e.g., settlement or overloading), or changes in material colour or texture suggesting dampness or chemical processes. All accessible structural elements are meticulously examined, including foundations (where accessible), basements, walls, floor slabs/ceilings, roof structures, balconies, windows, and doors.
Non-Destructive Testing (NDT) Methods
These methods allow us to assess the condition of materials and structures without causing any damage:
- Thermography: A thermal camera is used to capture temperature differences on surfaces. This helps identify areas of heat loss (thermal bridges), moisture-affected zones in walls or roofs (as moisture alters a material's thermal conductivity), air infiltration points, and occasionally even hidden structural elements or defects (e.g., infilled openings). When assessing heat loss and the presence of moisture, experts implicitly follow the principles found in LBN 002 'Thermal Performance of Building Envelopes'..
- Moisture Measurements: Specialised moisture meters (contact or non-contact) are used to determine moisture levels in various structural elements (timber, concrete, masonry). This aids in the identification of active leaks or condensation issues.
- Concrete Strength AssessmentUsing a Schmidt HammerSchmidt) or the ultrasonic pulse velocity method, concrete strength can be roughly assessed. This is particularly crucial in precast concrete panel buildings or monolithic concrete structures. This method often relies on approaches described in standard LVS EN 13791 'Assessment of concrete strength in structures and precast concrete components'.
- Reinforcement Detection: Electromagnetic instruments (cover meters) can determine the location of steel reinforcement (rebar) in concrete, its diameter, and the concrete cover thickness. This is critically important for assessing corrosion risk.
- Endoscopy: This involves inserting small cameras into hard-to-reach areas (e.g., behind cladding, in ventilation ducts) for visual condition assessment.
- Partially Destructive or Destructive Methods: These methods are applied less frequently, typically when NDT methods don't provide sufficient information or when a precise determination of material composition and properties is required. For example, break-out inspections (removing a small area of render or finishes) may be carried out to directly examine the structure, or material samples (e.g., concrete cores, timber samples) taken for laboratory analysis.
- Documentation Analysis: Reviewing the building design documentation, previous survey reports, and repair records can provide valuable insight into the building's original construction, any modifications made, and potential weak points.
Pre-war Brick Buildings (up to 1940)
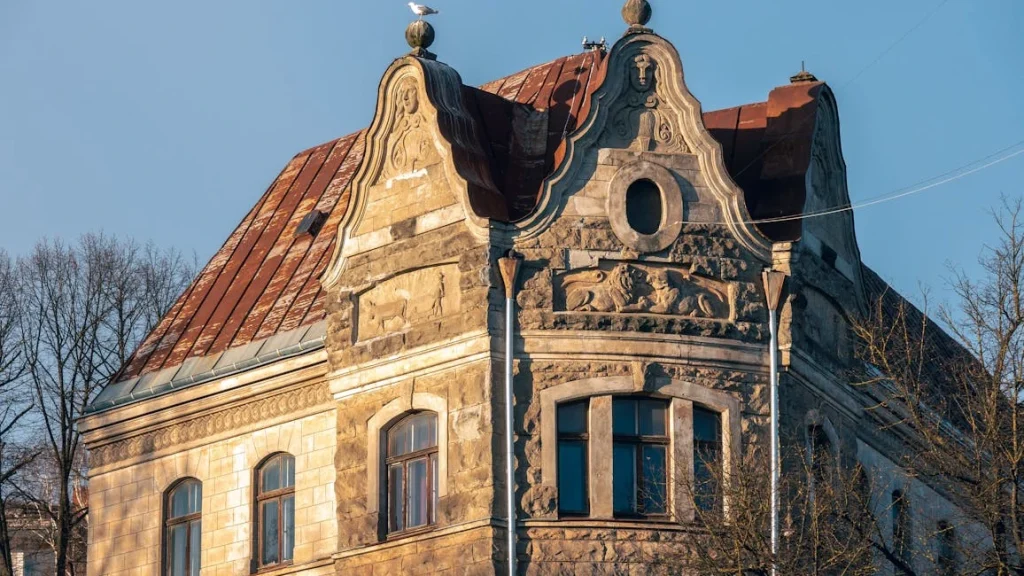
These buildings often charm with their architecture and robust construction, but decades of wear and tear inevitably take their toll.
- Foundation Issues: Expect to see settlement or deformation, often triggered by fluctuating groundwater levels, nearby construction work, vibrations, or simply the natural ageing of materials. This frequently manifests as cracks in walls, which are often diagonal around window and door openings. A lack of or damaged waterproofing commonly leads to dampness and salt efflorescence in basements and foundation masonry.
- Timber Floor and Beam Damage: Moisture ingress – from roof or service leaks, or condensation in basements and lofts – can lead to timber rot (the particularly dangerous true dry rot, or Serpula lacrymans) or wood-boring insect infestations (such as woodworm). Such damage can significantly reduce the load-bearing capacity of beams and is often difficult to detect without exposure or specialist inspection methods.
- Masonry Wall Defects: Over time, exposure to the elements (frost, rain, wind) can damage the joints in brick or stone masonry, causing the mortar to crumble. This allows moisture to penetrate the wall, leading to accelerated decay due due to repeated freeze-thaw cycles. Additionally, poorly executed historical repairs or alterations can create load redistribution issues and cracking.
- Chimney and Ventilation Duct Damage: Cracks, blockages, or a loss of airtightness in chimneys and ventilation ducts can not only cause draught issues but also pose a significant fire risk or lead to moisture condensation within the building's structures.
Soviet-Era Standard-Design Buildings (1950–1990)
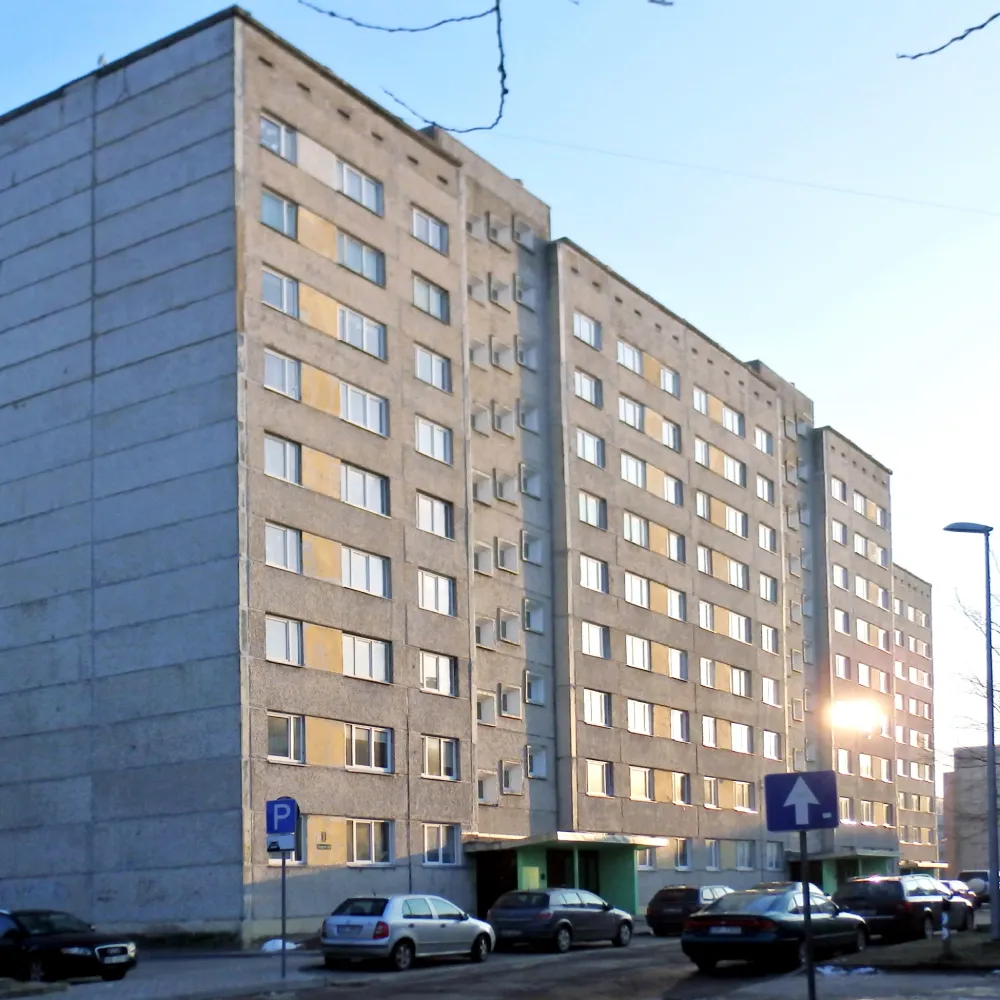
These are mass-scale constructions using standard designs, often focusing on speed and volume of build.
They are primarily reinforced concrete panel or brick buildings.
- Leaky Joints in External Wall Panels: This is one of the most widespread problems. Over time, the sealing mastic in the joints loses its elasticity, cracks, and allows moisture and cold air to penetrate. The consequences include mould in room corners, heat loss, and corrosion of the metal connecting elements within the panels.
- Damage to Balcony and Loggia Structures: Corrosion of the reinforcement bars due to insufficient concrete cover or moisture ingress leads to concrete spalling and cracking (which is particularly hazardous on the underside and edges of balcony slabs). There's also corrosion of handrail fixings.
- Flat Roof Problems: The lifespan of the waterproofing (often bitumen roll materials) is limited. Damage and improper drainage (such as clogged gutters or downpipes) lead to leaks on upper floors and moisture accumulation within the roof structure, damaging the thermal insulation and ceiling panels.
- Basement Flooding and Dampness: This is caused by insufficient or damaged waterproofing of foundations and basement walls, along with issues concerning rainwater or drainage systems.
- Deterioration of Utility Networks: Corrosion of pipelines (water, sewerage, heating) can cause leaks, leading to structural flooding.
It's important to note that many of these buildings have now reached or exceeded their projected service life of 50 years, as indicated by construction science research from Riga Technical University (Avotiņš, 2018).
New Builds (1991-2000)
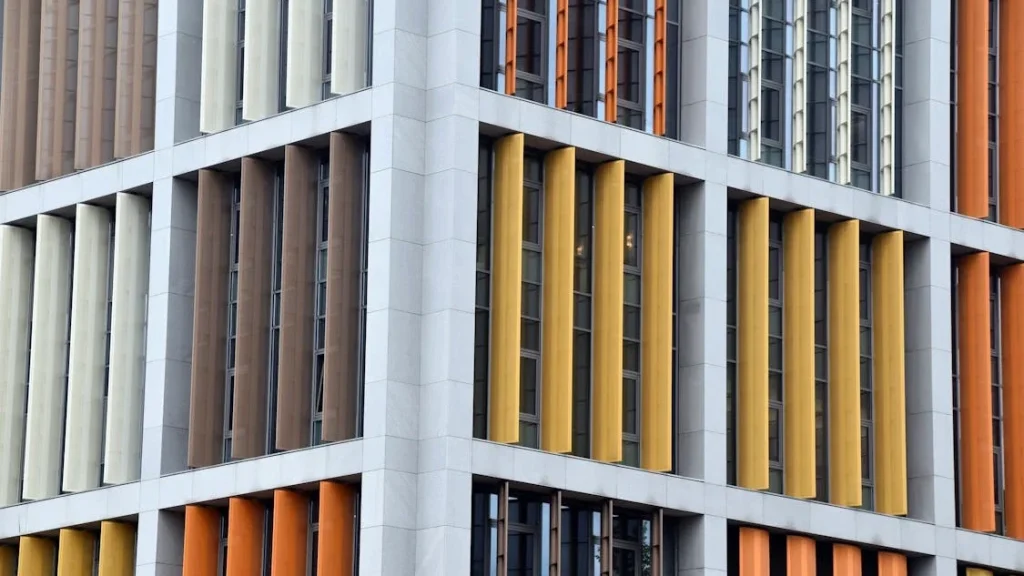
This period was characterised by a shift towards new materials and technologies, though at times it also saw a degree of chaos in the construction market and insufficient quality control.
- Quality issues with new materials: This included the incorrect use or installation of lightweight concrete (aerated concrete, foam concrete) blocks – for example, failing to observe the need for reinforcement or proper waterproofing, which could lead to cracking. There was also the use of cheap, poor-quality thermal insulation materials or their incorrect installation.
- Concreting defects: his involved an insufficient concrete cover for reinforcement, substandard concrete quality, or inadequate vibration during concreting, leading to voids.
- Waterproofing problems: Errors in the installation of waterproofing for foundations, basements, roofs, or terraces, often using new materials that weren't always correctly applied.
- Poor-quality installation: Mistakes in the installation of windows and doors, which caused heat loss and condensation. Also, incorrectly constructed roof covering joints or connections.
Summary
As is evident, every building type and age possesses its own unique "Achilles' heels". Hidden structural defects aren't merely a cosmetic nuisance; they can significantly impact your property's value, safety, and long-term maintenance costs. By commissioning a technical inspection of buildings and structures before purchasing a property, you gain a clear understanding of its true condition and can avoid very costly surprises in the future.
Conversely, for existing property owners, a regular technical inspection (for example, every 5-10 years, depending on the building's age and condition) helps to identify problems promptly and plan necessary repairs before they become critical.
Remember, a professional technical inspection of buildings and structures is not an unnecessary expense, but rather a wise investment in your property's safety and value preservation. Entrust this work only to certified and experienced construction experts who understand both the theory and Latvian construction practice, and who can "read" the building's story hidden beneath the plaster. To find out more about technical building inspections, please continue here.